So, it turns out there has not been a proper solar farm update since this one, back when we finally got the planning permission. It probably feels like nothing has happened since, which is more accurate than you might think, but stuff is changing much faster now, so time for an update!
For anyone new to the blog, I own a small company that is building a 1.2MWp solar farm in England as a side-project to making video games. 1.2MWp is tiny by solar farm standards, but it will power 300 homes, so its not *that* tiny. This is the first time I’ve ever got involved in any sort of ‘infrastructure’ project, so I’m learning as I go along…
I knew back in October when we got permission, that nothing was going to happen straight away, because any construction site that is in that part of England, in winter, in the rain and the mud and the rain and also in the rain… is basically untenable. I can not remember the exact number of large truckloads of equipment we need to get to this field, but I know its more like 30 than 20. Put that together with all the manpower that has to get there, and its just going to be an absolute mudslide of horrific proportions. When I first visited the site, the landowner met me on a quadbike, and I can see why…
(Imagine this…but with a thousand billion times more rain and mud)
Anyway, there was a lot of other stuff that needed doing before we actually stick things in the ground, so there has actually been some non-visible progress. Most of the progress was, sadly, in things I didn’t even know we needed.
The contractor who will build (and likely operate/maintain) the solar farm basically builds an array of low voltage (about 400v) solar panels, all of the inverters and the cabling to a substation. Thats basically all they do. They know how to wire up a LOT (3,024) of solar panels at a voltage of about 400v. Thats considered low voltage. The actual UK power grid at this size, tends to be operating at 11,000v (11kv) or 33kv or even higher. That means you need a transformer that steps up the voltage to 11kv, and switchgear that handles all that stuff. You then need to cable it from your substation to the DNO substation, which is where their responsibility begins.
It feels weird to me that this means 2 substations, but apparently it does. It also means that you need a high-voltage expert to design and handle all of the 11kv stuff, which goes beyond ‘ouch that hurts’ and right up to the ‘all that was left was the flaming boots’ level of danger, so I guess its no surprise you need a 3rd party expert for that stuff. Also I discovered that big transformers are full of oil. Who knew?
So…stuff has now got more complicated because the new structure of this project is now:
- Positech Energy (my company)
- The site construction contractor
- The landowner (farmer)
- The Distribution Network Operator or DNO (Grid people)
- High Voltage Consultant
No doubt during construction a bunch of other 3rd parties will be subcontracted to the construction contractor, but thats their problem. Also, eventually there will be an insurance company, plus the people who buy our electricity through a PPA (Power purchase agreement). Hilariously, that may happen through a PPA broker, so there may be yet another party involved. Are you starting to see where your electricity bill goes yet? :D
Anyway…so we now have a high voltage consultant who I deal with directly, but who has to liaise with the construction company and also the DNO, and this involves hilariously complicated email chains where everyone is waiting for everyone else until I step in and yell WHY IS NOTHING HAPPENING, but hopefully in a politer tone :D.
So…moving on from the fact that we now have a high voltage consultant, lets talk about all the other sudden expenses and complications. Ladies and gentleman, I introduce you to the excitement of pullout-tests. Apparently, you have to do pullout tests. Who knew? This is basically paying some engineering experts to go bang some metal posts into the field at a variety of points, then do their best to pull them out again, and measure how much force is required to pull them out. They use special machines and gadgets:
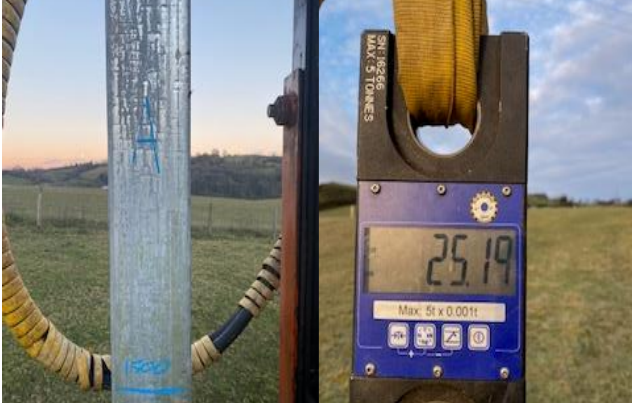
You get a rather tedious number of photos like this, and the eventual TL:DR; of it is that ‘its fine’ which is good to know, albeit a very unfulfilling way to spend £6,795. Yes really. You can buy a very nice guitar for that. Why are pullout tests needed? well they determine what kind of ground mount kit you will need to keep the panels in the ground. Why so important? well solar panels are actually pretty light, and catch the wind like crazy, and we have over 3,000 of them. We are basically anchoring a giant expensive sail to the top of a hill in the midlands. If we don’t secure these puppies nicely, we are just one storm away from them all turning up in Liverpool one day.
Anyway, after all the pain and stress of paying for pullout tests, comes the new excitement around earthing studies. Yes earthing studies. Did you not know solar farms need to be earthed! haha, you fool. Yes of course, we all knew that *loud coughing*. Its to stop a big lightning strike pulverizing the whole farm. Did I mention we are sticking 60 tons of solar panels on the top of a remote field? Anyway, in order to work out HOW to earth the farm, you need to know the resistance of the soil, which apparently, is a thing that varies.
A lot.
Anyway, thats of course another expense, and its all very depressing, and it takes time. Not only that, but TWO completely different companies carry out earthing designs for separate parts of the installation. The DNO (grid people) design the earthing for their substation, and our HV contractor designs the earthing for our bit. Its totally separate. This seems nuts to me, and ripe for optimisation, but I’m not an electrical engineer so maybe there are reasons for this.
Anyway, it means you get sent exciting diagrams like this:
I think we all understand this right? *louder coughing*. It also means you get a design for how all the fancy underground earthing stuff will be arranged, which is apparently generally in a grid pattern, presumably because you are earthing a LOT of stuff, and a single earth rod stuck in the ground isn’t going to cut it:
Oh, in other news I actually have the final quote for the install of the farm. I’ll give a proper breakdown once the farm is constructed, but you will enjoy the hilarity of reading about when I got the quote at 6PM on Friday, with a VERY ambiguous sentence in it, that led me to believe the farm was going to cost £450,000 more than I anticipated. I did not sleep at all Friday night, and was *relieved* on Monday when this was clarified.
Oh how we laughed
The final hilarious piece of news is that due to changes we had to make to the plant layout between getting planning permission refused, and then granted, I have 200 more solar panels than I need. I am still being charged monthly to store them, and this is not fun. I THINK I might be able to stick 8 of them in my driveway to replace my old 12 year old ones, but I’m not sure about that yet. The others will likely be sold to the construction company, at cost (still a net loss as I’ve stored them for 6 months+).
Anyway… the short version of this blog post is that there is PROGRESS. We are anticipating making the first 30% payment to the construction company today, which will mean we can plan actual install dates, and actually order the ground mount kit, inverters and other stuff like cabling. We will use 15km of DC solar cable, for example. Thats a lot of cable.
The good news is that stuff looks like its starting to actually happen now. I have been told that the cutout-switch has already arrived to the town next to the farm, and some other equipment used by the grid connection company has been ordered already. This is a very *good sign* as it means the grid connection will happen this decade, at least.
TL:DR; Gamedev is easy. Building stuff is hard.